2. На входе

Его масштабы поражают: размеры — 120 x 86 x 25 м, площадь силового пола — 10 000 м2, площадь силового потолка — 6 800 м2. Максимальная взлётная масса испытываемых самолётов — 500 тонн, их максимальные габариты — 80 x 80 x 20 м. При этом в статзале одновременно могут проходить испытания 10–12 самолётов и 15–20 агрегатов на отдельных стендах.
Конструкция корпуса-стенда, принятого в эксплуатацию в середине 60-х годов прошлого столетия, представляет собой комплекс из силового пола с влитым в прочный бетон множеством параллельных профилированных металлических желобов, набора мощнейших силовых колонн и силового потолка из продольных и поперечных балок, являющихся частями испытательных стендов. Колоссальное количество работающего металла!
А теперь, надев каску, познакомимся поближе с обитателями сего заведения.
3. Учебно-боевой истребитель Су-27УБ.
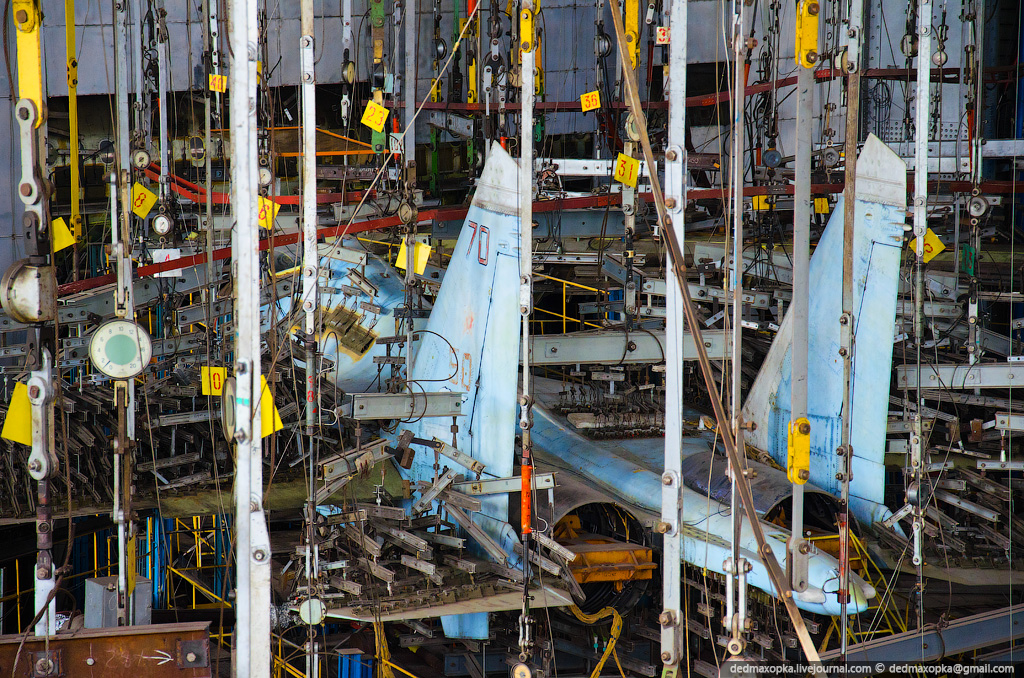
Он — один из первых в большом семействе «двадцать седьмых». Двухместный сверхзвуковой учебно-боевой истребитель. Первый полёт совершил в 1985 году. Конструкторы сохранили на нём в полном объёме бортовое радиоэлектронное оборудование и вооружение одноместной машины, получив в итоге полноценный боевой самолёт. Более того, наличие второго члена экипажа позволило в дальнейшем разработать двухместный многоцелевой истребитель Су-30 для ВВС и ПВО СССР, а на его базе — многочисленные модификации многофункционального истребителя Су-30К (МК), о котором расскажу ниже.
Экземпляр, прибывший в СибНИА на испытания, судя по виду, много и хорошо летал.
4. Су-27УБ в компании многоцелевого транспортного легкомоторного самолёта СМ-92Т «Супер Финист» (слева) и своего собрата Су-27СМ (справа вверху).
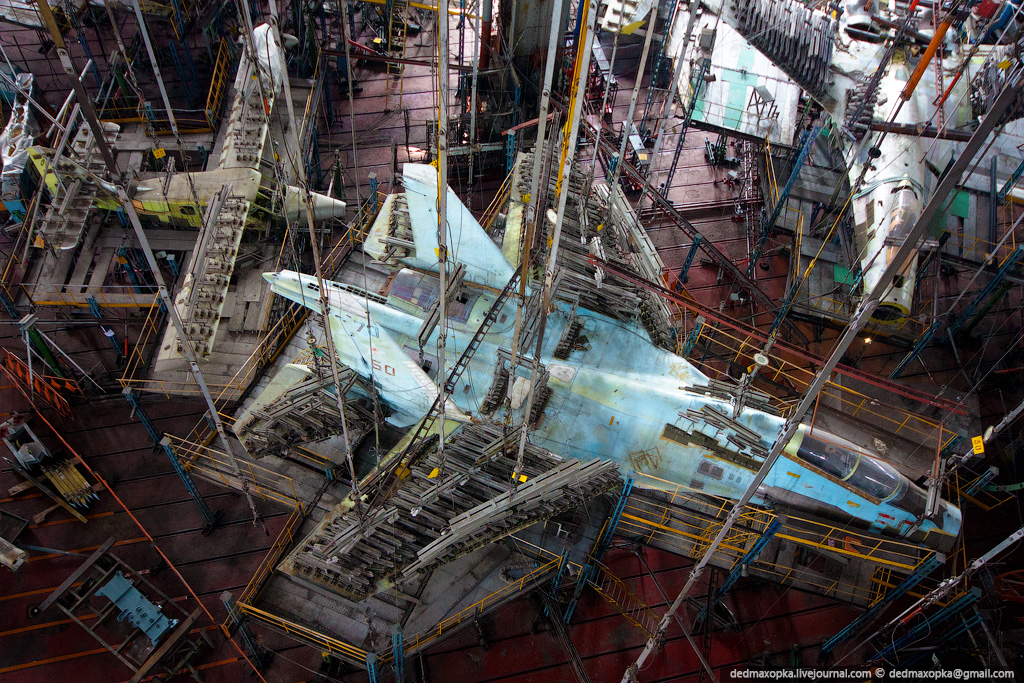
Снимок сделан с силового потолка статзала. Самолёт несёт на себе остатки вэ-вэ-эсовской окраски, с которой летал, пока не выработал установленный ресурс, был снят с эксплуатации и передан в СибНИА для установления остаточного ресурса и выработки рекомендаций по его продлению.
5. Вид с конца центральной хвостовой балки Су-27УБ.

Хорошо просматриваются термостойкие двигательные отсеки с имитаторами двигателей и прямоугольные гнёзда для патронов отстреливаемых ложных тепловых целей (ЛТЦ), иначе называемых «тепловыми ловушками», в автоматах сброса слева и справа от балки. В кадр попали нижние части двухкилевого вертикального оперения с рулями направления.
6. А это вид Су-27УБ в противоположном направлении — от кабины пилота в сторону хвостового оперения. Крылья завешаны рычaжкой и потому не видны.

7. Вот она, рычaжка, — во всей красе.

Это нагромождение металлических профилей, связанных между собой тягами разной длины, а с конструкцией самолёта — простыми брезентовыми лямками, приклеенными к обшивке «88-м» клеем, и называется звучным словом «рычaжка». Никакого хаоса — всё рассчитано и расположено точно по месту для адекватного воспроизведения эксплуатационных нагрузок. Представляете, каково эту прелесть монтировать?
Жгуты проводки у нижней части правого киля идут к датчикам системы тензометрирования.
8. А это снова рычaжка, но на левой консоли крыла Су-27УБ.

За рычaжкой видна носовая часть Су-27СМ с кабиной лётчика. Носовой радиопрозрачный обтекатель отстыкован. Чётко обозначено кольцо переднего силового шпангоута, принимающего на себя вес бортовой радиолокационной станции (БРЛС).
9. Глянем напоследок на Су-27УБ в проём силового потолка. Видны ровные оранжевые ряды полос листового металла, которыми местами зашиты за ненадобностью пазы в силовом полу статзала.
10. СМ-92Т «Супер Финист», Су-27УБ и Су-27СМ
11. Многоцелевой истребитель Су-27СМ.

Су-27СМ — результат проведённой глубокой модернизации известного на весь мир истребителя Су-27, предназначенного для завоевания превосходства в воздухе. Обновлённый самолёт стал многоцелевым, способным не только значительно эффективнее вести воздушный бой, но и работать по наземным и морским целям с использованием высокоточного управляемого оружия.
Программу модернизации для российских ВВС реализует КнААПО им. Ю. А. Гагарина.
Получив «стеклянную» кабину пилота с многофункциональными дисплеями, дополнительные точки подвески вооружения, двигатели с увеличенной тягой и усиленную конструкцию, самолёт потяжелел. А это прямой путь в СибНИА — на проверку его прочности.
12. Отсеки двигателей и центральная хвостовая балка Су-27СМ.

В отсеках видны весовые имитаторы двигателей АЛ-31Ф-М1 к которым крепятся тяги с динамометрами — элементы гидромеханической системы, воспроизводящей эксплуатационные нагрузки: тягу двигателя, силы, возникающие при манев-рировании ЛА и др.
13. Хвостовая часть Су-27СМ со снятым горизонтальным и вертикальным оперением.
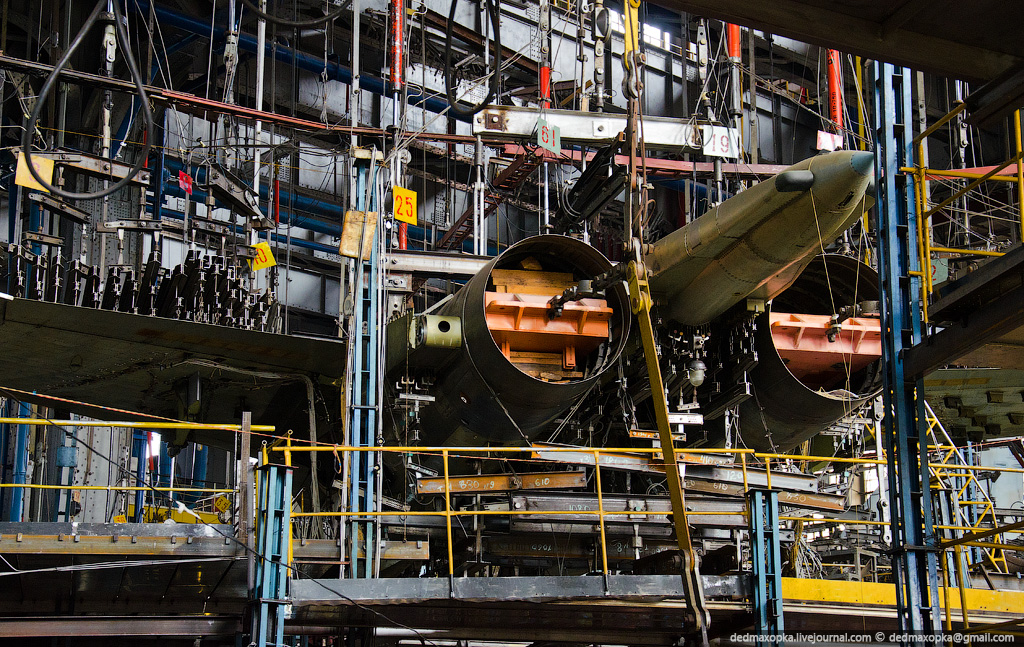
В процессе проведения испытаний по какой-то причине самолёт временно лишили хвостового оперения — килей и цельноповоротного горизонтального оперения.
14. Ещё один снимок стенда Су-27СМ.

На нём хорошо видны ярко-оранжевые гидроцилиндры одностороннего действия, жёлтые и серые тяги рычaжки, площадка для обслуживания стенда с жёлтыми перилами ограждения и синими стойками.
В отличие от стенда SSJ, в этом корпусе для воспроизведения знакопеременных нагрузок различной амплитуды и интенсивности рычaжка монтируется и на силовом полу, и на силовом потолке. Та её часть, которая смонтирована сверху, тянет, соответственно, вверх, а которая снизу самолёта — вниз. Вот таким способом он и «машет крыльями» по «прихоти» наших сибирских инженеров-испытателей.
15. Носовая часть Су-33. Вид спереди.

В тёмном углу статзала, спрятавшись за стендом для ресурсных испытаний механизации крыла пассажирского Ту-204, ожидает решения своей участи ещё один самолёт семейства Су-27 — палубный истребитель Су-33.
Их на службе у России осталось совсем немного. Да и плавучий аэродром у них тоже один — базирующийся в Заполярье тяжёлый авианесущий крейсер «Адмирал Флота Советского Союза Кузнецов» из состава Северного Флота.
Специфика полётов с палубы авианосца такова, что лётчики палубной авиации считаются элитой даже среди «своих».
17 июля 2001 года во время авиашоу, посвященного дню морской авиации, в районе гарнизона «Остров» в Псковской области на Су-33 (бортовой номер 70) погиб 47-летний Герой России заместитель командующего авиацией ВМФ страны генерал-майор Тимур Автандилович Апакидзе — один из первых строевых лётчиков, освоивших взлёты и посадки на па-лубу «Кузнецова», Человек, сделавший всё возможное для сохранения в России боевой палубной авиации, когда на ней в 90-е годы уже был поставлен жирный крест. Вечная память Герою…
Командующий авиацией ВМФ России и сам Министр обороны ныне озаботились проблемой вырабатывающих свой ресурс Су-33, и готовят им замену в виде новых многофункциональных истребителей МиГ-29К (корабельный) и МиГ-29КУБ (корабельный учебно-боевой).
16. Носовая часть Су-33. Вид сверху.

На тёмном фоне хорошо видны все элементы конструкции: белый радиопрозрачный обтекатель, переднее горизонтальное оперение (ПГО), иначе называемое дестабилизатором, и выпущенный воздушный тормоз на верхней поверхности центральной части фюзеляжа, а также ровные строчки заклёпок, выдающие места расположения силового набора — шпангоутов, стрингеров, нервюр, лонжеронов. Фонарь кабины пилота открыт.
Являясь «младшим братом» Су-27, самолёт, впервые поднявшийся в небо 17 августа 1987 года, значительно отличается от него в силу своеобразия условий эксплуатации и оснащён (как мы уже увидели) ПГО, крылом большей площади с мощной механизацией и складывающимися консолями, гаком для торможения с помощью тросов аэрофинишёра, системой дозаправки в воздухе, другими новшествами. Усилена конструкция его фюзеляжа и шасси.
На базе Су-33 разработан и построен один экземпляр Су-27КУБ — корабельного учебно-боевого двухместного варианта с продвинутой авионикой, авангардной аэродинамикой крыла с адаптивным профилем и пилотами, сидящими плечом к плечу, как на Су-24.
17. Вид на центроплан Су-33.

На этом снимке, как и на предыдущем, наблюдаем работающих на самолёте молодых специалистов, которых, как я заметил, в СибНИА достаточно много. И это хорошо! :) Есть кому принять «эстафету поколений» от ветеранов авиационной науки.
18. «Металлическое небо» над Су-33.

Этот экземпляр палубного истребителя никогда не поднимался в настоящее небо, не ощущал порывов холодного солёного ветра Северного Ледовитого океана, подрагивая от нетерпения в форсажном рёве турбин перед коротким разбегом по трамплину авианосца. Собранный на стапелях КнААПО им. Ю. А. Гагарина, он несёт крест своей судьбы в статзале СибНИА ради продления жизни своих собратьев и безопасности их пилотов.
19. Внешность обманчива — этот, спрятавшийся в грудах металлических конструкций симпатич-ный «утёнок» — ни кто иной, как грозный фронтовой бомбардировщик Су-34.

У Су-34 нелёгкая судьба. Это один из самых удачных образцов авиационной техники, родившихся ко времени развала Советского Союза и один из очень немногих, сумевших выжить, и превращающийся на наших глазах из «утёнка» в прекрасного «лебедя», постоянно совершенствуясь в процессе наземных и лётных испытаний.
Су-34, только начинающий свою серийную биографию, как и Су-24, в течение десятилетий являющийся одним из самых многочисленных самолётов в парке ВВС, — это высокоинтеллектуальные продукты прославленного КБ Павла Осиповича Сухого и одного из крупнейших авиастроительных предприятий страны — НАПО им. В. П. Чкалова, набирающего темп серийного производства отставшей было на старте от своих соперников многообещающей машины.
Разработка Т-10В началась 19 июня 1986 года, первый полёт Т10В-1 — прототипа Су-34 (или, иначе, Су-27ИБ — истребителя-бомбардировщика) состоялся 13 апреля 1990 года, а первый серийный Су-34 (Т-10В-5) поднялся в воздух с аэродрома Новосибирского авиазавода ещё 28 декабря 1994 года.
Как вы поняли, индексы «Т» присваиваются опытным изделиям ОКБ Сухого.
Освоение серийного производства шло очень тяжело в силу вполне понятных причин, связанных с затянувшимся кризисом в стране.
Являясь потомком Су-27, он значительно отличается от него конструктивно. Бросается в глаза неповторимый рисунок обводов передней части фюзеляжа, вместившего в себя объёмную двухместную кабину для пилотов, сидящих рядом плечом к плечу, как на предшественнике Су-24, для замены которого Су-34 создан. Впервые на подобном типе боевого самолёта экипажу созданы достаточно комфортные условия для выполнения многочасовых дальних полётов.
20. Вид на нижнюю поверхность правой части центроплана, корневой наплыв крыла, воздухозаборник правого двигателя Су-34. Не переднем плане можно хорошо рассмотреть элементы рычaжки. Всё гениальное — просто: нарезанные по размеру металлические детали, брезент, деревянные палочки, клей. :)

21. По этому профилированному каналу воздух поступает в двигатель Су-34. Двигатель отсутствует, поэтому «виден свет в конце канала».
22. А вот и Су-30МК, «как на ладони».

Как обещал, знакомлю вас с многоцелевым (многофункциональным) истребителем Су-30МК (модернизированный коммерческий), предназначенным для поставок на экспорт.
Разработан на базе Су-30К (коммерческий) — варианта двухместного истребителя-перехватчика на базе Су-27УБ с систе-мами дозаправки топливом в полёте и спутниковой навигации (GPS).
Первый полёт совершил в 1993 году. Является одной из самых удачных моделей боевого ударного авиационного комплекса поколения 4+. Имеет многочисленные модификации «заточенные» под требования национальных ВВС различных государств: Су-30МКА (модернизированный, коммерческий, алжирский), Су-30МКИ (… индийский), Су-30МКК (… китайский), Су-30МКМ (… малазийский), Су-30МКВ (… венесуэльский), Су-30М2 и Су-30СМ (для ВВС России), Су-30КН — ещё один коммерческий вариант.
На экспортных модификациях Су-30 широко применяется бортовое оборудование иностранного производства.
Специалисты СибНИА готовятся сейчас к проведению ресурсных испытаний этого самолёта.
23. Су-30МК, вид сзади.

24. Изящество железной птицы.

Аэродинамическая компоновка, придающая самолёту неповторимый облик, отрабатывалась при непосредственном участии специалистов СибНИА.
На снимке хорошо видны стойки шасси (передняя и две основные) с красными дисками имитаторов колёс, открытые створки их ниш, оклонённый предкрылок на правой консоли крыла (слева), правая консоль ПГО (дестабилизатора, в центре), воздухозаборники (под ней) с заглушками, открытый фонарь двухместной кабины экипажа (вверху справа). Окраска самолёта яркая, почти новая.
На заднем плане слева (точно над правым неокрашенным килём самолёта) можно рассмотреть ажурные стыки силовых колонн и продольных балок силового потолка статзала.
25. Передняя стойка шасси и входы воздухозаборников Су-30МК.

26. Места в статзале заняты «согласно купленным билетам». В первом ряду слева-направо: многоцелевой транспортный легкомоторный самолёт СМ-92Т «Супер Финист» производства Смоленского авиазавода, разработанный НПФ «Техноавиа», и Су-27УБ производства Иркутского авиационного завода (ИАЗ), во втором ряду — Су-34 производства НАПО и (за колонной) многоцелевой Су-80ГП производства КнААПО.
27. Посмотрим поближе на Су-80ГП.

Он — один из немногих представителей гражданских машин ОКБ Сухого. Это многоцелевой грузопассажирский двухбалочный триплан с турбовинтовыми двигателями и П-образным хвостовым оперением. Первый полёт совершил 4 сентября 2001 года.
Оснащён герметичным салоном на 30 пассажиров. Может перевозить до 3300 кг груза на расстояние до 1300 километров. Быстро преобразуется из пассажирского варианта в грузовой и обратно. Грузовая рампа в хвостовой части фюзеляжа позволяет транспортировать лёгкую автомобильную технику и стандартные авиационные контейнеры.
Красивый самолёт для местных и региональных воздушных линий, предназначенный для замены Ан-24, Ан-26, Як-40. Но, «не родись красивым, а родись счастливым» — пока его судьба складывается не очень удачно…
На переднем плане снимка — аккуратный нос Су-34 с радиопрозрачным обтекателем.
28. А здесь в строгом порядке хранятся стойки, тяги, гидроцилиндры и другие детали испытательных стендов. Беспорядок в авиации недопустим (в СибНИА, по крайней мере, под руководством директора — лётчика-испытателя 1 класса, стараются это правило строго выполнять).

29. За панелями огромного защитного короба находится магистральный пассажирский самолёт Ту-204.

Прозванный на Западе «Тихим бизоном» за малошумные отечественные двигатели (а говорим, что всё у нас плохо), очень летучий (с прекрасной аэродинамикой) самолёт родился в тяжёлое время — на рубеже 80-х и 90-х годов, а попал на испытания в СибНИА в 1993 году. Оттого на них и задержался…
В проёме защитного экрана видна зона сочленения центроплана и фюзеляжа, на переднем плане — пилон с оранжевым имитатором двигателя, отклонённые секции предкрылка.
30. Силовой потолок. Между силовым потолком и крышей работают крановщицы (сейчас их в кабинах кранов нет — обеденный перерыв). Внизу в проёме виден силуэт Су-30МК.

Силовой потолок корпуса-стенда № 6 СибНИА представляет собой настоящее произведение инженерного искусства и строительной доблести. Проект корпуса разработан специалистами Новосибирского филиала проектного научно-исследовательского института Министерства авиационной промышленности СССР — ГипроНИИавиапрома.
Прежде чем уйти из статзала, предлагаю вашему вниманию
виртуальный тур. Это мой первый опыт, потому интересна критика.
32. Отблеск космических зорь.

В зале ресурсных испытаний SSJ, недалеко от стенда, хранятся исторические реликвии — киль воздушно-космического самолёта (ВКС) «Буран» (с демонтированной левой половиной двухстворчатого двухсекционного руля направления, выполнявшего одновременно функцию воздушного тормоза) и транспортный контейнер (на снимке слева, зелёный) для перевозки посадочного модуля пилотируемого космического корабля Л-3 — соперника американского «Аполлона».
Мало кто знает, что впервые с «космосом» СибНИА познакомился в начале 60-х годов, когда институту было поручено проведение теплопрочностных испытаний ракетного блока «Е» посадочного модуля лунного корабля Л-З разработки КБ «Южное». Испытания проводились с воспроизведением всех факторов многосуточного космического полёта и дали хороший результат. При этих испытаниях моделировались тепловые и механические воздействия на блок при различных режимах его работы на Луне (посадка днём или ночью, отказ от посадки, аварийный или штатный старт с Луны днём или ночью и др.). Температурные воздействия реализовывались в диапазоне температур от –170 до +950°С с высокими ско-ростями нагрева и охлаждения.
Если бы не проблемы с ракетой-носителем Н-1, наши космонавты побывали бы на Луне ещё сорок лет назад! Однако, в 1974 году советская пилотируемая лунная программа была закрыта и работы по этой тематике прекращены.
Позднее, с середины 1976 года, СибНИА стал заниматься работами по «Бурану».
Проводились испытания крупных агрегатов и элементов конструкции ВКС, плиточной теплозащиты на комплексное воздействие механических, тепловых и акустических нагрузок, в том числе с имитацией условий космической среды. Так, носок крыла испытывался в диапазоне температур от –120 до +1300°С и давлении от 10–3 мм рт. ст. до атмосферного.
В работах по «Бурану» были задействованы многие специалисты СибНИА. Так, прочнисты принимали активное участие в создании и статических испытаниях гермокабины, проводили расчёты прочности её конструкции. Аэродинамики изучали взлётно-посадочные характеристики, а также аэродинамические характеристики ВКС на траектории спуска.
Оценку их работам дал сам «Буран», выполнивший 15 ноября 1988 года триумфальный беспилотный космический полёт.
Кстати, американцы повторили подобное на своём экспериментальном космическом беспилотном орбитальном самолёте «Boeing X-37» через 22 года — в 2010-м.
Приглашаю вас посетить ещё один огромный испытательный корпус под номером 30.
33. «Тридцатка».

Его так и называют в СибНИА — «тридцатка». Портрет возвышающегося над окружающими строениями гиганта таков: размеры 100 x 70 x 30 м, площадь силового пола —5 400 м2, максимальная взлётная масса испытываемых самолётов —400 тонн, их максимальные габариты — 90 x 90 x 20 м.
Снимок в достаточной степени передаёт масштабы сооружения, введённого в эксплуатацию в начале 80-х годов прошлого столетия. Слева располагается летающая лаборатория Як-40, принадлежащая лётно-исследовательской базе (ЛИБ) СибНИА. За ней справа в глубине корпуса — стенд ресурсных испытаний самолёта-заправщика Ил-78 с колоннадой.
Обычная панельная конструкция корпуса № 30 не позволяет использовать её в качестве силового каркаса так, как мощную конструкцию корпуса № 6. Поэтому приходится монтировать громадные стенды из типовых элементов по принципу трансформера.
34. Ресурсный стенд Ил-78.

Ресурсные испытания самолёта-заправщика Ил-78 с бортовым номером 76607 были начаты в СибНИА 1987 году.
На снимке видна левая консоль крыла самолёта с двумя пилонами, на которых закреплены имитаторы двигателей Д-30КП-2 (красные). Справа от стенда — вторые, «северо-восточные» ворота корпуса.
Ил-78, совершивший первый полёт в 1983 году, создан на базе военно-транспортного самолёта Ил-76М и предназначен для дозаправки в воздухе военных самолётов во время дальних беспосадочных полётов. Его новая версия Ил-78М (М — модернизированный, создан на базе Ил-76МД, первый полёт в 1987 году) оснащена тремя унифицированными подвесными агрегатами заправки (УПАЗ) и способна передавать в воздухе заправляемым самолётам 105,7 тонн топлива, заправляя, например, три истребителя Су-30 одновременно.
35. «Калиточка».

Огромные ворота корпуса № 30 служат для ввоза поступивших на испытания «изделий».
В 80-е годы весь статзал был занят испытываемой авиационной техникой, в 90-е годы испытания были остановлены из-за отсутствия финансирования и корпус был законсервирован. Сейчас появилась перспектива его использования, связанная с разработанными специалистами СибНИА проектами ремоторизации самолётов местных воздушных линий Ан-2 и Як-40.
36. Железный цветок.

На снимке — лопатки первой ступени компрессора турбореактивного двигателя TFE341-3 фирмы «Honeywell Aerospace» (США), которым предполагается заменить двигатели АИ-25 на самолёте Як-40, получив в результате улучшение его эксплуатационных характеристик.
Но это — ближайшая перспектива, а на сей день уже реализован проект по ремоторизации легендарного «кукурузника» Ан-2, разработанного в середине 40-х годов прошлого столетия коллективом Олега Константиновича Антонова с участием специалистов СибНИА и являющегося рекордсменом по продолжительности серийного производства и времени эксплуатации — около 65-ти лет!
Замена поршневого АШ-62ИР, производство которого уже давно прекращено, на газотурбинный двигатель ТРЕ331-12 той же фирмы «Honeywell Aerospace» позволило улучшить характеристики воздушного судна.
«Словно с „москвича“ пересел на иномарку», — так описывают свои ощущения, касающиеся техники пилотирования самолёта, лётчики-испытатели и пилоты гражданской авиации, выполнявшие полёты на Ан-2МС, отмечая при этом низкую утомляемость экипажа по сравнению с Ан-2 в связи с меньшими уровнями шума и вибраций в кабине. Отбор тёплого воздуха позволяет поддерживать в кабине экипажа и в пассажирском салоне комфортные условия даже на высоте 4000 м при температуре наружного воздуха –35°С. Перебалансировка самолёта при изменении режима силовой установки намного меньше чем на Ан-2. Исчезла необходимость постоянно следить за температурой головок цилиндров и регулировать её, чего требовал от пилотов прежний поршневой двигатель АШ-62ИР.
Переместимся по территории СибНИА в корпус № 4Б.
37. Динамические испытания основной стойки шасси Ту-204СМ.

Шасси самолётов испытывают колоссальные нагрузки при посадке. Особенно, если она проходит нештатно.
При испытаниях взлётно-посадочных устройств ЛА в институте используются стенды (копры) разной размерности и, соответственно, разных воспроизводимых усилий, имитирующих условия реальных посадок, послепосадочного пробега и руления по аэродромам с их неровностями и другими проблемами.
На снимке — подъём основной стойки шасси нового магистрального пассажирского самолёта Ту-204СМ, закреплённой на клети, перед сбросом на неподвижную опору копра К-30 с весом сбрасываемого груза до 30 тонн. Сам момент сброса я заснять не успел — настолько быстро он произошёл. Грохот от удара стойки об опору был очень сильным. Представляю, как «звучат» испытания на копре К-100 с неподвижной опорой, проходящие с раскруткой колёс до посадочных скоростей, или на копре К-80 с массивным барабаном 4-метрового диаметра, раскручивающимся для имитации бетонной взлётно-посадочной полосы, набегающей на садящийся со скоростью до 380 км/ч самолёт!
38. Копры К-30 и К-80.

Прочнисты СибНИА отметились в следующих работах, потребовавших приложения огромных усилий, существенных финансовых вложений, воплотившихся в создании и многолетней эксплуа-тации уникальных заловстендов и комплексов оборудования, с которыми я вас только что познакомил:
Обеспечение прочности и долговечности большинства серийных гражданских и военных самолётов и вертолётов, созданных в СССР и России.
Проведение исследований, обеспечивающих надёжность и прочность взлётно-посадочных устройств (шасси) всех самолётов, созданных в СССР и России.
Разработка оригинальной методики испытаний авиакосмических объектов (например, ВКС «Буран») без использования высокотемпературных вакуумных камер.
Разработка оригинальной методики акустических испытаний объектов авиакосмической техники на основе эффекта бегущей акустической волны.
Есть ещё много чего достигнутого коллективом Сибирского НИИ авиации за его 70-летнюю историю, но в изложении это выглядит для неспециалистов ещё более заумно, потому ограничусь сказанным.
39. А на «десерт» — изображение символа преданности делу, закреплённого на лацкане пиджака одного из ведущих специалистов СибНИА в области прочности авиаконструкций, попросившего не раскрывать его имени. Что ж, скромность всегда украшала настоящих мужчин.

Если мой рассказ о СибНИА вам понравился, буду рад его продолжить — ведь на сегодня за кадром остались разработка, постройка и восстановление летательных аппаратов, интереснейшие лётные испытания (в том числе восстановленных самолётов времён Великой Отечественной войны) и ещё ряд направлений работы уникального предприятия, являющегося одним из крупнейших научно-исследовательских центров отечественной авиационной отрасли.
Есть ещё ряд задумок, связанных с новой и интересной для меня авиационной темой, которые, если осуществятся, будут приятным сюрпризом для всех, включая меня самого. :)
Если хотите узнать о СибНИА больше прямо сейчас, тогда вам сюда:
www.sibnia.ruВыражаю благодарность руководству СибНИА за организацию фотосъемок. Отдельное спасибо Калюте Андрею Андреевичу за помощь в написании текста и интересную компанию!